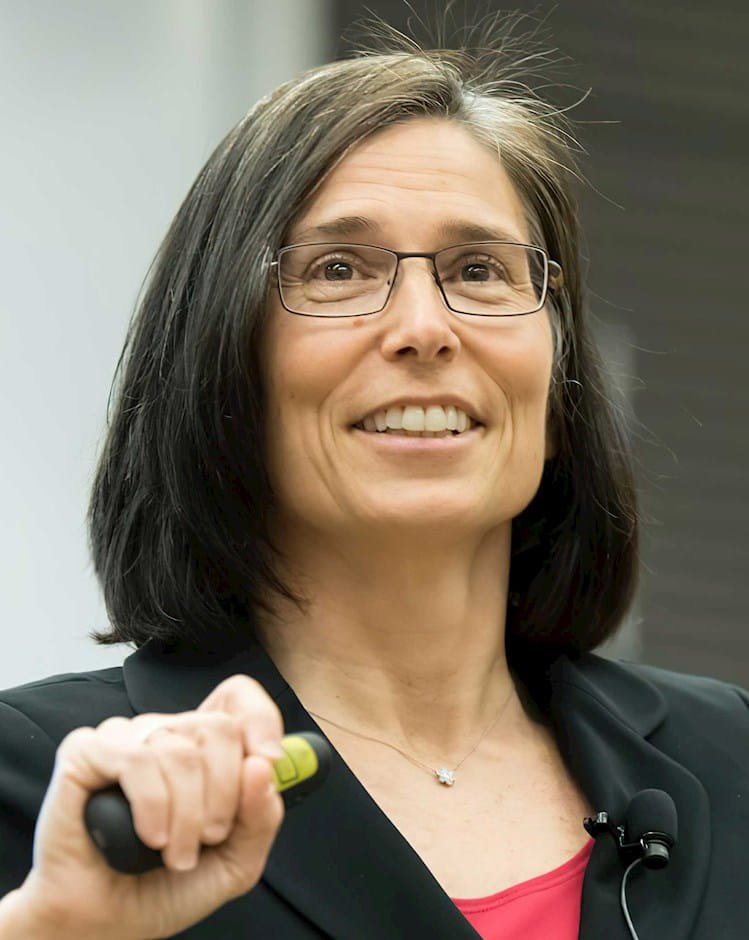
Nicole DeHoratius
Adjunct Professor of Operations Management
Adjunct Professor of Operations Management
Nicole received her D.B.A from Harvard Business School, her M.Sc. from the University of Sussex as a Rotary Ambassadorial Scholar, and her A.B., magna cum laude, from Harvard College. She joined Chicago Booth in 2001 and since then has taught operations management, service operations, and supply chain management to executives in programs and companies around the globe. For exemplifying the characteristics students most value in their professors, Nicole earned the 2015 and 2016 Rotman School of Management Teaching Award.
REVISION: The Past, Present, and Future of Retail Analytics: Insights from a Survey of Academic Research and Interviews with Practitioners
Date Posted:Thu, 04 Aug 2022 07:19:43 -0500
We document the evolution of academic research through a bibliometric analysis of 123 retail analytics articles published in top operations management journals from 2000-2020. We isolate nine decision areas via manual coding that we verify using automated text analysis (topic modeling). We track variation across decision areas and method-usage evolution per analytics type, featuring the degree to which big data (e.g., clickstream, social media, product reviews) and analytics suited for these new data sources (e.g., machine learning) are used. Our analysis reveals a rapidly growing field that is evolving in terms of content (decisions, retail sector), data, and methodology. To determine the state of practice, we interviewed global practitioners on the current use of retail analytics. These interviews shed light on the barriers and enablers of adopting advanced analytics in retail. They also highlight what sets companies on the frontier (e.g., Amazon, Alibaba, Walmart) apart from the ...
REVISION: Customer Preferences for Delivery Service Attributes in Attended Home Delivery
Date Posted:Wed, 27 Jul 2022 13:46:29 -0500
Retailers face increasing competitive pressure to determine how best to deliver products purchased online to the end customer. Grocery retailers often require attended home delivery where the customer must be present to receive the delivery. For attended home delivery to function, the retailer and customer must agree upon a delivery time slot that works for both parties.
Using online data from a grocery retailer, we observe customer preferences for three delivery service attributes associated with each time slot: speed, precision, and timing. We define speed as the expected time between the placement of an order and its delivery, precision as the duration of the offered time slot, and timing as the availability of choices across times of the day and days of the week. We show that customers not only value speed as an attribute of delivery service but that precision and timing are also key drivers of the customers time slot selection process.
We also observe substantial customer ...
REVISION: The Past, Present, and Future of Retail Analytics: Insights from a Survey of Academic Research and Interviews with Practitioners
Date Posted:Tue, 19 Jul 2022 05:55:27 -0500
We document the evolution of academic research through a bibliometric analysis of 123 retail analytics articles published in top operations management journals from 2000-2020. We isolate nine decision areas via manual coding that we verify using automated text analysis (topic modeling). We track variation across decision areas and method-usage evolution per analytics type, featuring the degree to which big data (e.g., clickstream, social media, product reviews) and analytics suited for these new data sources (e.g., machine learning) are used. Our analysis reveals a rapidly growing field that is evolving in terms of content (decisions, retail sector), data, and methodology. To determine the state of practice, we interviewed global practitioners on the current use of retail analytics. These interviews shed light on the barriers and enablers of adopting advanced analytics in retail. They also highlight what sets companies on the frontier (e.g., Amazon, Alibaba, Walmart) apart from the ...
REVISION: The Past, Present, and Future of Retail Analytics: Insights from a Survey of Academic Research and Interviews with Practitioners
Date Posted:Mon, 02 May 2022 13:02:16 -0500
We document the evolution of academic research through a bibliometric analysis of 123 retail analytics articles published in top operations management journals from 2000-2020. We isolate nine decision areas via manual coding that we verify using automated text analysis (topic modeling). We track variation across decision areas and method-usage evolution per analytics type, featuring the degree to which big data (e.g., clickstream, social media, product reviews) and analytics suited for these new data sources (e.g., machine learning) are used. Our analysis reveals a rapidly growing field that is evolving in terms of content (decisions, retail sector), data, and methodology. To determine the state of practice, we interviewed global practitioners on the current use of retail analytics. These interviews shed light on the barriers and enablers of adopting advanced analytics in retail. They also highlight what sets companies on the frontier (e.g., Amazon, Alibaba, Walmart) apart from the ...
REVISION: The Past, Present, and Future of Retail Analytics: Insights from a Survey of Academic Research and Interviews with Practitioners
Date Posted:Fri, 29 Apr 2022 14:40:15 -0500
We document the evolution of academic research through a bibliometric analysis of 123 retail analytics articles published in top operations management journals from 2000-2020. We isolate nine decision areas via manual coding that we verify using automated text analysis (topic modeling). We track variation across decision areas and method-usage evolution per analytics type, featuring the degree to which big data (e.g., clickstream, social media, product reviews) and analytics suited for these new data sources (e.g., machine learning) are used. Our analysis reveals a rapidly growing field that is evolving in terms of content (decisions, retail sector), data, and methodology. To determine the state of practice, we interviewed global practitioners on the current use of retail analytics. These interviews shed light on the barriers and enablers of adopting advanced analytics in retail. They also highlight what sets companies on the frontier (e.g., Amazon, Alibaba, Walmart) apart from the ...
REVISION: Evaluating Count Prioritization Procedures for Improving Inventory Accuracy in Retail Stores
Date Posted:Wed, 30 Mar 2022 18:35:58 -0500
Problem definition: We compare several approaches for generating a prioritized list of items to be counted in a retail store, with the objective of detecting inventory record inaccuracy and unknown out-of-stocks. We consider both “rule-based” approaches, which sort items based on heuristic indices, and “model-based” approaches, which maintain probability distributions for the true inventory levels updated based on sales and replenishment observations.
Methodology/results: Our study evaluates these approaches on multiple metrics using data from inventory audits we conducted at European home and personal care retailer dm-drogerie markt. Our results support arguments for both rule-based and model-based approaches. We find that model-based approaches provide versatile visibility into inventory states and are useful for a broad range of objectives, but that rule-based approaches are also effective as long as they are matched to the retailer’s goal. We find that “high-activity” ...
REVISION: Evaluating Count Prioritization Procedures for Improving Inventory Accuracy in Retail Stores
Date Posted:Mon, 29 Nov 2021 08:29:18 -0600
We compare several approaches for generating a prioritized list of products to be counted in a retail
store, with the objective of detecting inventory record inaccuracy and unknown out-of-stocks. Our study evaluates these approaches using data from inventory audits we conducted at European home and personal care retailer dm-drogerie markt. We consider both \rule-based" approaches, which sort products based on heuristic indices, and \model-based" approaches, which maintain probability distributions for the true inventory levels updated based on sales and replenishment observations. Our results support arguments for both rule-based and model-based approaches. We nd that model-based approaches provide versatile visibility into inventory states and are useful for a broad range of objectives, but that rule-based approaches are also effective as long as they are matched to the retailer's goal. We find that "high-activity" rule-based policies that favor items with high sales volumes, ...
REVISION: Modeling the Behavior of Patients Who Leave the Emergency Department Without Being Seen
Date Posted:Mon, 01 Nov 2021 19:29:15 -0500
Queue abandonment has a significant impact on system performance. However, the key drivers for abandonment, particularly in observable systems, are not well understood. To better inform our understanding of abandonment behavior, we study the effect of three operational drivers of abandonment from a hospital emergency department (ED), namely, waiting time, queue length, and observed service rate. We confirm that all three factors affect a patient's propensity for leaving the waiting area without being seen by a physician (LWBS), i.e., abandoning the queue. Further, these factors interact with each other in a non-linear fashion. Both ED crowding and observed service rate influence a patient's perception of waiting time. Moreover, patients are not homogenous in their abandonment response and we observe behavior that is distinct for patients with severe conditions. Specifically, patients who report to a congested ED with more severe conditions are more inclined to abandon the ED early in ...
New: Retail Store Operations: Literature Review and Research Directions
Date Posted:Mon, 01 Nov 2021 09:58:57 -0500
In the digital age, retail store operations face a variety of novel challenges and complexities. We review 255 papers on retail store operations from 32 operations research, management science, retailing, and general management journals over the period 2008–2016. We assess the current state of research within the context of retail store operations. By discussing the limitations present in these papers, we identify a number of research gaps and propose several opportunities for advancing retail expertise in the operations management community. Full paper available at ...
REVISION: Retail Analytics: The Quest for Actionable Insights from Big Data on Consumer Behavior and Operational Execution
Date Posted:Tue, 22 Jun 2021 09:41:03 -0500
We document the development of academic research on retail analytics and compare it with current practice. We provide a definition of retail analytics, describe its evolution, and conduct bibliometric analyses on 123 retail analytics articles published in top operations journals in the 2000-2020 period. Our work distinguishes nine different analytical decision areas as well as types of analytics used. To document the current state of retail practice, we interviewed global practitioners, asking them to highlight their transitions from basic to advanced analytics. We conclude with a roadmap advising future research on retail analytics, including a discussion of how to better facilitate the adoption of academic work in practice.
REVISION: Execution Failures in Retail Supply Chains - A Virtual Reality Experiment
Date Posted:Wed, 09 Sep 2020 03:44:26 -0500
Problem definition: Increasingly, retail store employees find themselves being asked to pick orders from inventory. These tasks are performed under intense conditions and, in many cases, are made more difficult because of high product variety and high degrees of product similarity.
Academic/Practical relevance: It is important to provide quantifiable information about the impact of task complexity and task intensity on worker performance and understand how actions can boost productivity and reduce errors.
Methodology: We conduct a real-effort task in a virtual environment where subjects are to sort cubes into bins. We study task complexity by varying the degree of similarity between the cubes and task intensity by varying the arrival pace of the cube. Beyond traditional descriptive performance analysis we also analyze subjects' movements.
Results: Reducing task complexity by making the cubes more distinct increases productivity by as much as 38.2% and reduces the ...
REVISION: Evaluating Count Prioritization Procedures for Improving Inventory Accuracy in Retail Stores
Date Posted:Fri, 31 Jul 2020 03:44:17 -0500
We compare several approaches for generating a prioritized list of products to be counted in a retail store, with the objective of detecting inventory record inaccuracy and unknown out-of-stocks. We consider both "rule-based" approaches, which sort products based on heuristic indices, and "model-based" approaches, which maintain probability distributions for the true inventory levels updated based on sales and replenishment observations. Our study evaluates these approaches on multiple metrics using data from inventory audits we conducted at European home and personal care retailer dm-drogerie markt. Our results support arguments for both rule-based and model-based approaches. We find that model-based approaches provide versatile visibility into inventory states and are useful for a broad range of objectives, but that rule-based approaches are also effective as long as they are well-matched to the retailer's goal.
REVISION: Evaluating Count Prioritization Procedures for Improving Inventory Accuracy in Retail Stores
Date Posted:Thu, 30 Jul 2020 09:30:42 -0500
We compare several approaches for generating a prioritized list of products to be counted in a retail store, with the objective of detecting inventory record inaccuracy and unknown out-of-stocks. We consider both "rule-based" approaches, which sort products based on heuristic indices, and "model-based" approaches, which maintain probability distributions for the true inventory levels updated based on sales and replenishment observations. Our study evaluates these approaches on multiple metrics using data from inventory audits we conducted at European home and personal care retailer dm-drogerie markt. Our results support arguments for both rule-based and model-based approaches. We find that model-based approaches provide versatile visibility into inventory states and are useful for a broad range of objectives, but that rule-based approaches are also effective as long as they are well-matched to the retailer's goal.
REVISION: Customer Preferences for Delivery Service Attributes in Attended Home Delivery
Date Posted:Mon, 04 May 2020 10:21:35 -0500
Retailers face increasing competitive pressure to determine how best to deliver products purchased on-line to the end customer. As online retailing grows, so does the need for retailers to establish an appropriate fulfillment strategy. This is particularly true in grocery where the customer must be present to receive perishable goods from the retailer. Attended home delivery requires the retailer and the customer to agree upon a delivery time slot that works for both parties. Customers may exhibit different preferences for the selection of a delivery time slot. Using data from a grocery retailer that performs attended home deliveries, we evaluate customer responses to three delivery attributes, namely, speed, precision, and flexibility. We define speed as the expected time between the placement of an order and delivery, precision as the duration of the offered time slot, and flexibility as the availability of choices across times of the day and days of the week. Our results ...
REVISION: Execution Quality and Chargeback Penalties in Retail Supply Chains
Date Posted:Mon, 30 Mar 2020 10:29:41 -0500
Retailers procure inventory by placing purchase orders (POs) with suppliers. POs specify product price, quantity, quality, delivery times, and other aspects of the fulfillment process, such as carton labeling requirements and packaging formats. When servicing an order, a supplier may fail to meet the fulfillment terms, thus committing a fulfillment error and triggering a chargeback penalty. We collect supplier compliance manuals from 111 retailers to characterize fulfillment errors and chargebacks in practice. The majority of chargeback penalties listed by retailers pertain to execution quality: aspects of the fulfillment process beyond product price, quantity, quality, and delivery time. We use an empirically grounded analytical model in combination with game-theoretic analysis to demonstrate that the chargebacks most commonly used in practice do a poor job coordinating supply chains around execution quality. This result contradicts the recommendations in the trade literature.
REVISION: Execution Quality and Chargeback Penalties in Retail Supply Chains
Date Posted:Tue, 25 Feb 2020 11:07:57 -0600
Retailers procure inventory by placing purchase orders (POs) with suppliers. POs specify product price, quantity, quality, delivery times, and other aspects of the fulfillment process, such as carton labeling requirements and packaging formats. When servicing an order, a supplier may fail to meet the fulfillment terms, thus committing a fulfillment error and triggering a chargeback penalty. We collect supplier compliance manuals from 111 retailers to characterize fulfillment errors and chargebacks in practice. The majority of chargeback penalties listed by retailers pertain to execution quality: aspects of the fulfillment process beyond product price, quantity, quality, and delivery time. We develop a model to study the effectiveness of chargeback penalties as coordination mechanisms for execution quality. We identify the extent to which chargeback penalties coordinate a supply chain on execution quality and find that common chargebacks that retailers use in practice do not ...
REVISION: Execution Quality and Chargeback Penalties in Retail Supply Chains
Date Posted:Wed, 20 Nov 2019 10:35:03 -0600
Retailers procure inventory by placing purchase orders (POs) with suppliers. POs specify product price, quantity, quality, delivery times, and other aspects of the fulfillment process, such as carton labeling requirements and packaging formats. When servicing an order, a supplier may fail to meet the fulfillment terms, thus committing a fulfillment error and triggering a chargeback penalty. We collect supplier compliance manuals from 111 retailers to characterize fulfillment errors and chargebacks in practice. The majority of chargeback penalties listed by retailers pertain to execution quality: aspects of the fulfillment process beyond product price, quantity, quality, and delivery time. We develop an empirically rounded model to study the effectiveness of chargeback penalties as coordination mechanisms for execution quality. First, we assess whether the chargeback penalties retailers use in practice accurately convey the cost of execution quality errors from the retailer to the ...
REVISION: Execution Quality and Chargeback Penalties in Retail Supply Chains
Date Posted:Thu, 16 May 2019 07:33:12 -0500
Retailers procure inventory by placing purchase orders (POs) with suppliers. POs specify product price, quantity, quality, delivery times, and other aspects of the fulfillment process, such as carton labeling requirements and packaging formats. Suppliers’ adherence to fulfillment terms enables retailers’ supply chain optimizations, e.g., automation and pack-by-store flow. When servicing an order, a supplier may fail to meet the fulfillment terms, thus committing a fulfillment error and triggering a chargeback penalty. Chargebacks reduce supplier revenues, transferring billions of dollars from suppliers to retailers annually. We collect supplier compliance manuals from 111 retailers to characterize fulfillment errors and chargebacks in practice. The majority of chargeback penalties listed by retailers pertain to execution quality: aspects of the fulfillment process beyond product price, quantity, quality, and delivery time. Hence, chargebacks can act as mechanisms for firms to ...
REVISION: Modeling the Behavior of Patients Who Leave the Emergency Department Without Being Seen
Date Posted:Mon, 06 May 2019 10:45:44 -0500
Queue abandonment has a significant impact on system performance. However, the key drivers for abandonment, particularly in observable systems, are not well understood. To better inform our understanding of abandonment behavior, we study the effect of three operational drivers of abandonment from a hospital emergency department (ED), namely, waiting time, queue length, and observed service rate. We confirm that all three factors affect a patient's propensity for leaving the waiting area without being seen by a physician (LWBS), i.e., abandoning the queue. Further, these factors interact with each other in a non-linear fashion. Both ED crowding and observed service rate influence a patient's perception of waiting time. Moreover, patients are not homogenous in their abandonment response and we observe behavior that is distinct for patients with severe conditions. Specifically, patients who report to a congested ED with more severe conditions are more inclined to abandon the ED early in ...
REVISION: Modeling the Behavior of Patients Who Leave the ED Without Being Seen
Date Posted:Mon, 06 May 2019 08:29:48 -0500
Queue abandonment has a significant impact on system performance. However, the key drivers for abandonment, particularly in observable systems, are not well understood. To better inform our understanding of abandonment behavior, we study the effect of three operational drivers of abandonment from a hospital emergency department (ED), namely, waiting time, queue length, and observed service rate. We confirm that all three factors affect a patient's propensity for leaving the waiting area without being seen by a physician (LWBS), i.e., abandoning the queue. Further, these factors interact with each other in a non-linear fashion. Both ED crowding and observed service rate influence a patient's perception of waiting time. Moreover, patients are not homogenous in their abandonment response and we observe behavior that is distinct for patients with severe conditions. Specifically, patients who report to a congested ED with more severe conditions are more inclined to abandon the ED early in ...
REVISION: Execution Quality and Chargeback Penalties in Retail Supply Chains
Date Posted:Fri, 14 Sep 2018 05:27:51 -0500
Retailers procure inventory by placing purchase orders (POs) with suppliers. POs specify product price, quantity, quality, and delivery times as well as other aspects of the fulfillment process, such as carton labeling requirements and packaging formats. Retailers expect suppliers to adhere to fulfillment terms to enable supply chain optimizations, e.g., automation and pack-by-store product flows. When servicing an order, a supplier may fail to adhere to the fulfillment terms, thus committing a fulfillment error and triggering a chargeback penalty. Chargebacks reduce supplier revenues, transferring billions of dollars from suppliers to retailers annually. We collect supplier compliance manuals from 111 retailers to characterize fulfillment errors and chargeback penalties in practice. We find that the majority of chargeback penalties listed by retailers pertain to execution quality: i.e., aspects of the fulfillment process beyond product price, quantity, quality, and delivery time. ...
REVISION: Execution Failures in Retail Supply Chains - A Virtual Reality Experiment
Date Posted:Fri, 31 Aug 2018 09:45:19 -0500
We conduct a real-effort experiment in an immersive virtual environment and quantify the impact of product similarity on operational execution in a retail setting. In our experiments, subjects must identify and sort two types of products based on their observable characteristics. We find measures of operational execution to be substantially lower when the observable characteristics of the two products types are very similar compared to when they are dissimilar. Specifically, we observe more sorting errors and more products left unsorted when subjects handle products with more similar observable characteristics. Introducing a visual cue to distinguish products improves execution when the products are dissimilar (by lowering the frequency of sorting mistakes) and, even more so, when they are similar (by reducing both the number of sorting mistakes and the number of products left unsorted). Overall performance (measured by the faction of products correctly sorted) increases by ...
Update: Modeling the Behavior of Patients Who Leave the ED Without Being Seen
Date Posted:Sun, 09 Jul 2017 11:59:14 -0500
Abandonment in queues has long been recognized as having a significant impact on system performance. Nevertheless, our empirical understanding of the key drivers for abandonment, particularly in observable systems, is limited. Most models of abandonment assume that it occurs after a length of time sampled from an exogenous distribution, with no dependence on the system. However, discrete-event simulation, a commonly used tool for decision making in service systems, permits much more complex (and hence accurate) models of abandonment than those simply based on time in system. To better inform our understanding of abandonment and guide our modeling of this behavior, we study three operational drivers of abandonment, namely, waiting time, queue-length, and service rate. Using operational data from a hospital emergency department, we show that all three factors affect a patient’s propensity for leaving the waiting area without being seen by a physician (LWBS). Further, these factors ...
New PDF Uploaded
Update: Execution Quality and Chargeback Penalties in Retail Supply Chains
Date Posted:Thu, 22 Jun 2017 06:51:47 -0500
Retailers procure inventory by placing purchase orders (POs) with suppliers. POs specify product price, quantity, quality, and delivery times as well as other aspects of the fulfillment process, such as bar code standards and placement, carton labeling requirements, and packaging format. Retailers expect suppliers to adhere to fulfillment terms to enable supply chain optimizations, e.g., automation and pack-by-store product flows. When servicing an order, a supplier may fail to adhere to the fulfillment terms, thus committing a fulfillment error and triggering a chargeback penalty. Chargebacks reduce supplier revenues, transferring billions of dollars from suppliers to retailers annually. We collect supplier compliance manuals from 111 retailers to characterize fulfillment errors and chargeback penalties in practice. We find that the majority of chargeback penalties listed by retailers pertain to execution quality: i.e., aspects of the fulfillment process beyond product price, ...
New PDF Uploaded
Update: Fulfillment Errors and Chargeback Penalties in Retail Supply Chains
Date Posted:Thu, 22 Jun 2017 06:46:07 -0500
Retailers replenish inventory by placing purchase orders (POs) with suppliers. POs specify product order quantities and delivery times as well as many other aspects of the fulfillment process, such as bar code standards and placement, carton labeling requirements, hanger styles, and product packaging. Retailers expect suppliers to adhere to these fulfillment terms in order to optimize their supply chains, employ automation, or manage pack-by-store product flows. When fulfilling an order, a supplier may commit a fulfillment error, i.e., the supplier may fail to adhere to the specified terms. Although fulfillment errors are common, retailers can correct the majority of fulfillment errors through rework. Herein, we study the cost impact of correctable fulfillment errors. We demonstrate that the commonly used incentive to prevent fulfillment errors - chargebacks - do not impose penalties aligned with the true cost of fulfillment errors in this retail context. Overall, our research ...
New PDF Uploaded
New: Execution Quality and Chargeback Penalties in Retail Supply Chains
Date Posted:Wed, 21 Jun 2017 22:13:26 -0500
Retailers procure inventory by placing purchase orders (POs) with suppliers. POs specify product price, quantity, quality, and delivery times as well as other aspects of the fulfillment process, such as bar code standards and placement, carton labeling requirements, and packaging format. Retailers expect suppliers to adhere to fulfillment terms to enable supply chain optimizations, e.g., automation and pack-by-store product flows. When servicing an order, a supplier may fail to adhere to the fulfillment terms, thus committing a fulfillment error and triggering a chargeback penalty. Chargebacks reduce supplier revenues, transferring billions of dollars from suppliers to retailers annually. We collect supplier compliance manuals from 111 retailers to characterize fulfillment errors and chargeback penalties in practice. We find that the majority of chargeback penalties listed by retailers pertain to execution quality: i.e., aspects of the fulfillment process beyond product price, ...
REVISION: Consistency and Recovery in Retail Supply Chains
Date Posted:Wed, 21 Jun 2017 09:34:22 -0500
Practitioners and researchers describe inventory service level with metrics that communicate the likelihood of demand fulfillment without considering the on-going capabilities of the supplier, e.g., in-stock and _ll rate. We develop a method for measuring inventory service level that incorporates such supplier capabilities, namely consistency (the ability of a supplier to fulfill orders repeatedly) and recovery (the ability of a supplier to fulfill orders after a lapse in service). Using data from two retail supply chains, we illustrate our approach. To demonstrate the impact of consistency and recovery on supply chain performance, we model a retailer purchasing from competing suppliers with different levels of consistency and recovery. The model incorporates the retailer's uncertainty about demand and the retailer's uncertainty about its suppliers' service levels. We characterize how the retailer's orders and profitability change with a supplier's delivery performance through ...
REVISION: Fulfillment Errors and Chargeback Penalties in Retail Supply Chains
Date Posted:Wed, 03 Aug 2016 05:50:27 -0500
Retailers replenish inventory by placing purchase orders (POs) with suppliers. POs specify product order quantities and delivery times as well as many other aspects of the fulfillment process, such as bar code standards and placement, carton labeling requirements, hanger styles, and product packaging. Retailers expect suppliers to adhere to these fulfillment terms in order to optimize their supply chains, employ automation, or manage pack-by-store product flows. When fulfilling an order, a supplier may commit a fulfillment error, i.e., the supplier may fail to adhere to the specified terms. Although fulfillment errors are common, retailers can correct the majority of fulfillment errors through rework. Herein, we study the cost impact of correctable fulfillment errors. We demonstrate that the commonly used incentive to prevent fulfillment errors - chargebacks - do not impose penalties aligned with the true cost of fulfillment errors in this retail context. Overall, our research ...
REVISION: Consistency and Recovery in Retail Supply Chains
Date Posted:Wed, 29 Jun 2016 09:55:07 -0500
Practitioners and researchers describe inventory service level using uni-dimensional metrics, e.g., in-stock and fill rate. However, prior research identifies dynamic aspects of supplier performance: consistency (the ability of a supplier to fulfill orders repeatedly) and recovery (the ability of a supplier to fulfill orders after a lapse in service). We develop a method for measuring consistency and recovery, and we test the method in the retail supply chain context using more than 40,000 order and fulfillment records provided by suppliers to retailers in two distinct settings. We model a retailer purchasing from competing suppliers with different levels of consistency and recovery. This model incorporates the retailer's uncertainty about demand and the retailer's uncertainty about its suppliers' service levels, which the retailer assesses using each supplier's prior performance. We characterize how the retailer's orders change with a supplier's performance through numerical ...
REVISION: Consistency and Recovery in Retail Supply Chains
Date Posted:Thu, 31 Mar 2016 04:06:12 -0500
We extend prior research on retailers ordering from unreliable suppliers to incorporate dynamic aspects of supplier performance identified in the literature: consistency (the ability of a supplier to fulfill orders repeatedly) and recovery (the ability of a supplier to fulfill orders after a lapse in service). We develop a method for measuring consistency and recovery, and we test the method using more than 40,000 order and fulfillment records collected from two suppliers to retailers (387 SKUs over 268 weeks). We propose a model of a retailer purchasing from two competing suppliers with different levels of consistency and recovery. The model incorporates both the retailer's uncertainty about its demand and the retailer's uncertainty about its suppliers' reliabilities, which the retailer assesses using each supplier's prior performance. We use the empirical data to conduct numerical experiments with the model that characterize how the retailer's orders change with a supplier's ...
REVISION: Modeling the Behavior of Patients Who Leave the ED Without Being Seen
Date Posted:Wed, 24 Feb 2016 11:20:50 -0600
Abandonment in queues has long been recognized as having a significant impact on system performance. Nevertheless, our empirical understanding of the key drivers for abandonment, particularly in observable systems, is limited. Most models of abandonment assume that it occurs after a length of time sampled from an exogenous distribution, with no dependence on the system. However, discrete-event simulation, a commonly used tool for decision making in service systems, permits much more complex (and hence accurate) models of abandonment than those simply based on time in system. To better inform our understanding of abandonment and guide our modeling of this behavior, we study three operational drivers of abandonment, namely, waiting time, queue-length, and service rate. Using operational data from a hospital emergency department, we show that all three factors affect a patient’s propensity for leaving the waiting area without being seen by a physician (LWBS). Further, these factors ...
REVISION: The Impact of Supplier Inventory Service Level on Retailer Demand
Date Posted:Thu, 14 Jan 2016 06:54:36 -0600
To set inventory service levels, suppliers must understand how changes in inventory service level affect demand. We build on prior research, which uses analytical models and laboratory experiments to study the impact of a supplier's service level on demand from retailers, by testing this relationship in the field. We analyze a field experiment at the supplier Hugo Boss to deter- mine how the supplier's inventory service level affects demand from its retailer customers. We find increases in historical fill rate to be associated with statistically significant and managerially substantial increases in current retailer orders (i.e., demand, not just sales). Specifically, a one percentage point increase in fill rate, measured over the prior year, is associated with a statistically significant 11% increase in current retailer demand, controlling for other factors that might affect retailer demand. We explore the drivers of this demand increase, including changes in retailer assortment and ...
REVISION: The Impact of Supplier Inventory Service Level on Retailer Demand
Date Posted:Thu, 22 Oct 2015 01:20:35 -0500
To set inventory service levels, suppliers must understand how changes in inventory service level affect demand. We build on prior research, which uses analytical models and laboratory experiments to study the impact of a supplier's service level on demand from retailers, by testing this relationship in the field. We analyze a field experiment at the supplier Hugo Boss to determine how the supplier's inventory service level affects demand from its retailer customers. We find that increases in historical service level are associated with statistically significant and managerially substantial increases in current retailer orders (i.e., demand, not just sales). Specifically, a one percentage point increase in fill rate, measured over the prior year, is associated with a statistically significant 11% increase in current retailer demand, controlling for other factors that might affect retailer demand. We explore the drivers of this demand increase, including changes in retailer assortment ...
REVISION: Understanding the Behavioral Drivers of Execution Failures in Retail Supply Chains: An Experimental Study Using Virtual Reality
Date Posted:Tue, 20 Oct 2015 05:51:02 -0500
We conduct a real-effort experiment in an immersive virtual environment in order to quantify the role of product similarity in execution failures in a retail setting. In our experiments, subjects must identify and sort two types of products based on their observable characteristics. When the two products are very similar, performance is substantially lower (with both more sorting errors and more products left unsorted) than when the products are more dissimilar. Introducing a clear visual cue to distinguish the products improves execution when the products are dissimilar (by lowering sorting mistakes) and, even more so, when they are similar (both by reducing sorting mistakes and the number of products unsorted). In the latter case the average increase in overall performance is over 22 percentage points. Our results suggest that there may be important gains from taking ease of execution into account in the design of products, product packaging, and labeling.
REVISION: Inventory Management with Fulfillment Errors and Rework
Date Posted:Thu, 30 Jul 2015 11:39:37 -0500
Retailers replenish inventory by placing purchase orders (POs) with suppliers. POs stipulate terms for fulfillment beyond order quantity and delivery time, such as specifications for electronic data interchange, carton labeling, and retail tickets. These fulfillment terms are instrumental for optimized supply chains employing automation and techniques such as pack-by-store. When fulfilling an order, a supplier may commit a fulfillment error, i.e., the supplier may fail to adhere to the terms specified by the PO. Prior research has shown that the retailer can correct the majority of fulfillment errors through rework. In this article, we study how inventory policy and cost change in the presence of such correctable fulfillment errors. Further, we examine how retailers respond to fulfillment errors in practice by characterizing commonly used penalties, or chargebacks. Our research provides guidance to managers seeking to mitigate fulfillment errors and demonstrates that chargebacks ...
New: Execution Quality: An Analysis of Fulfillment Errors at a Retail Distribution Center
Date Posted:Fri, 03 Jul 2015 01:08:41 -0500
Purchase orders specify many aspects of the fulfillment process, including item quantity, delivery time, carton labeling, bar coding, electronic data interchange, retail ticketing, and others. These fulfillment terms are instrumental for highly optimized supply chains employing automation and techniques such as pack-by-store. When fulfilling a purchase order, a supplier may commit a fulfillment error, i.e., the supplier may fail to adhere to the terms specified by the relevant contract. We present a study of the fulfillment errors that occur in practice using data collected from a major retailer's distribution center. While fulfillment errors involving incorrect product quantities and delivery times have received the most attention in the literature, we find that the majority of fulfillment errors in the context we study involve documentation, bar coding, and retail ticketing. We refer to these as correctable fulfillment errors, since they are amended at the retailer's distribution ...
REVISION: The Impact of Supplier Inventory Service Level on Retailer Demand
Date Posted:Tue, 05 May 2015 07:47:20 -0500
To set inventory service levels, suppliers must understand how changes in inventory service level affect demand. Although researchers have studied the impact of a supplier's service level on its demand using analytical models and laboratory experiments, this relationship has not, to the best of our knowledge, been tested in the field. We study how the supplier Hugo Boss's inventory service level affects demand from its retail customers. We find increases in historical service level to be associated with statistically significant and managerially substantial increases in current retailer orders (i.e., demand, not just sales). Specifically, upon controlling for other factors that might affect retailer demand, we find a 1 percent increase in this supplier's type 1 service level measured over the prior year to be associated with a 13 percent increase in current retailer demand. Further, we find that retailers that order frequently exhibit a larger reaction to changes in service level, an ...
REVISION: Modeling the Behavior of Patients Who Leave the ED Without Being Seen
Date Posted:Wed, 17 Dec 2014 01:13:16 -0600
Abandonment in queues has long been recognized as having a significant impact on system performance. Yet, our empirical understanding of the key drivers for abandonment, particularly in observable systems, is limited. Furthermore, most models of abandonment assume that it occurs after a length of time sampled from an exogenous distribution, with no dependence on the system. However, discrete-event simulation, a commonly used tool for decision making in service systems, permits much more complex (and hence accurate) models of abandonment than those simply based on time in system. This paper studies three key drivers of abandonment, namely, waiting time, queue-length, and service rate, which are also tractable for modeling. Using operational data from a hospital emergency department, we show that all three factors affect a patient’s propensity for leaving the waiting area without being seen by a physician (LWBS). Further, these factors interact with each other in a non-linear fashion. ...
New: Execution Quality: An Analysis of Fulfillment Errors in a Retail Distribution Center
Date Posted:Wed, 17 Dec 2014 01:10:19 -0600
Purchase orders specify many aspects of the fulfillment process, including item quantity, delivery time, carton labeling, bar coding, electronic data interchange, retail ticketing, and others. These fulfillment terms are instrumental for highly optimized supply chains employing automation and techniques such as pack-by-store. When fulfilling a purchase order, a supplier may commit a fulfillment error, i.e., the supplier may fail to adhere to the terms specified by the relevant contract. We present a study of the fulfillment errors that occur in practice using data collected from a major retailer's distribution center. While fulfillment errors involving incorrect product quantities and delivery times have received the most attention in the literature, we find that the majority of fulfillment errors in the context we study involve documentation, bar coding, and retail ticketing. We refer to these as correctable fulfillment errors, since they are amended at the retailer's distribution ...
New: Inventory Management with Purchase Order Errors and Rework
Date Posted:Fri, 15 Aug 2014 02:34:57 -0500
Shipments received by retail distribution centers may contain errors that retailers can correct through rework. A ticket error, for example, occurs when the tickets attached to some items within a purchase order (PO) display incorrect information, such as selling price, and can be amended by affixing corrected tickets. Ticket errors and other PO fulfillment errors, discussed herein, are costly and different from traditional random yields. This paper describes the prevalence of PO errors at a large retail chain and studies the cost of PO errors to a standard inventory system. In so doing, this research provides guidance to retailers seeking to collaborate with vendors to reduce errors, set appropriate chargebacks to incentivize vendors, or modify their inventory policy to account for PO errors.
REVISION: The Impact of Supplier Inventory Service Level on Retailer Demand in the Supply Chain for Functional Apparel Items
Date Posted:Wed, 13 Aug 2014 22:52:37 -0500
To set inventory service levels, firms must understand how changes in inventory service level affect customer demand. While the effects of service level changes have been studied empirically at the level of the end consumer, relatively little is known about the interaction between a retailer and a supplier. Using data from a supplier of branded apparel, we show increases in inventory service level to be associated with statistically significant and substantial increases in retailer orders (i.e., demand, not just sales). Controlling for other factors that might affect demand, we find a 1 percent increase in historical inventory service level to be associated with a 13 percent increase in demand from retailers, where historical service level is the type 1 service level performance of the apparel manufacturer over the prior year. Further, retailers that order frequently exhibit a larger reaction to changes in service level, an outcome that is consistent with retailers learning about and ...
REVISION: Modeling the Behavior of Patients Who Leave the Emergency Department Without Being Seen by a Physician
Date Posted:Wed, 23 Apr 2014 03:36:03 -0500
We present an empirical study of an emergency department in which patients may leave the waiting area without being seen by a physician (LWBS patients). Using operational data from a hospital emergency department, we show that both time and number of patients in the waiting area significantly increase a patient’s LWBS probability. These factors interact with each other in a non-linear fashion. In addition to these two factors, we show that observed service rate affects LWBS probability, where the magnitude of its effect depends on waiting time. As waiting time increases, higher observed service rates may encourage patients to wait. We also examine the shape of the hazard rate curves for LWBS behavior. We use these findings to draw insights into modeling LWBS behavior. We discuss the state-of-the art for existing queueing and simulation models of abandonment and translate how our findings affect the utility of these models; the results point to the need for further model development.
New: Inventory Management with Purchase Order Errors and Rework
Date Posted:Tue, 13 Aug 2013 03:22:00 -0500
In a retail distribution center, the fulfillment of a purchase order (PO) occasionally arrives with errors that the retailer can correct through rework. PO fulfillment errors, which we will refer to as PO errors in brevity henceforth, include “ticket errors,” in which an incorrect stock keeping unit (SKU) number or sale price is put on the tickets attached to some items in a PO. These errors are different from the random yield errors well-known in the literature. Using data from a large ...
New: Inventory Management with Purchase Order Errors and Rework
Date Posted:Thu, 08 Aug 2013 14:11:27 -0500
In a retail distribution center, the fulfillment of a purchase order (PO) occasionally arrives with errors that the retailer can correct through rework. PO fulfillment errors, which we will refer to as PO errors in brevity henceforth, include “ticket errors,” in which an incorrect stock keeping unit (SKU) number or sale price is put on the tickets attached to some items in a PO. These errors are different from the random yield errors well-known in the literature. Using data from a large ...
REVISION: The Impact of Supplier Reliability on Retailer Demand
Date Posted:Fri, 03 May 2013 13:45:37 -0500
To set inventory service levels, firms must understand how changes in service level affect customer demand. While the effects of service level changes have been studied empirically at the level of the end consumer, relatively little is known about the interaction between a retailer and a supplier. Using data from a manufacturer of branded apparel, we show increases in service level to be associated with statistically significant increases in retailer orders (i.e., demand, not just sales) ...
New: Inventory Management with Purchase Order Errors and Rework
Date Posted:Wed, 12 Dec 2012 10:56:05 -0600
In a retail distribution center, the fulfillment of a purchase order (PO) occasionally arrives with errors that the retailer can correct through rework. PO fulfillment errors, which we will refer to as PO errors in brevity henceforth, include “ticket errors,” in which an incorrect stock keeping unit (SKU) number or sale price is put on the tickets attached to some items in a PO. These errors are different from the random yield errors well-known in the literature. Using data from a large ...
REVISION: Point-of-Care Testing: Improving Emergency Department Performance through Process Redesign
Date Posted:Sat, 08 Dec 2012 04:01:04 -0600
Hospital emergency departments (EDs) typically rely on central laboratories to analyze patient samples for the purposes of diagnosing and treating patients. Point-of-care testing (POCT) is a process redesign that shifts the analysis of samples from the central lab to the ED. Using a queueing model, we generate hypotheses about how POCT impacts operational performance and then test those hypotheses empirically using data collected from a large, urban, tertiary, academic hospital. Specifically, ...
REVISION: Point-of-Care Testing: Improving Emergency Department Performance through Process Redesign
Date Posted:Thu, 11 Oct 2012 11:50:34 -0500
Hospital emergency departments (EDs) typically rely on central laboratories to analyze patient samples for the purposes of diagnosing and treating patients. Point-of-care testing (POCT) is a process redesign that shifts the analysis of samples from the central lab to the ED. Using a queueing model, we generate hypotheses about how POCT impacts operational performance and then test those hypotheses empirically using data collected from a large, urban, tertiary, academic hospital ...
New: Inventory Management with Purchase Order Errors and Rework
Date Posted:Tue, 07 Feb 2012 06:44:34 -0600
In a retail distribution center, the fulfillment of a purchase order (PO) occasionally arrives with errors that the retailer can correct through rework. PO fulfillment errors, which we will refer to as PO errors in brevity henceforth, include “ticket errors,” in which an incorrect stock keeping unit (SKU) number or sale price is put on the tickets attached to some items in a PO. These errors are different from the random yield errors well-known in the literature. Using data from a large retail ...
New: Inventory Management with Purchase Order Errors and Rework
Date Posted:Wed, 14 Dec 2011 15:20:11 -0600
In a retail distribution center, the fulfillment of a purchase order (PO) occasionally arrives with errors that the retailer can correct through rework. PO fulfillment errors, which we will refer to as PO errors in brevity henceforth, include “ticket errors,” in which an incorrect stock keeping unit (SKU) number or sale price is put on the tickets attached to some items in a PO. These errors are different from the random yield errors well-known in the literature. Using data from a large retail ...
REVISION: The Impact of Supplier Reliability Tracking on Customer Demand: Model and Estimation Methodology
Date Posted:Wed, 13 Jul 2011 15:37:53 -0500
To set service levels, firms must understand how changes in service affect customer demand. Supplier reliability tracking is a process whereby customers use past supplier performance to build beliefs about supplier capabilities and hence about future supplier performance. This paper presents a multi-period model of suppliers selling substitutable products to a customer that engages in supplier reliability tracking. Using this analytical model, we observe how a supplier's service level ...
REVISION: The Impact of Supply Learning on Customer Demand: Model and Estimation Methodology
Date Posted:Fri, 24 Sep 2010 16:07:32 -0500
To set service levels, firms must understand how changes in service affect customer demand. Supply learning is a process whereby customers use past supplier performance to build beliefs about supplier capabilities and hence about future supplier performance. This paper presents a multi-period model of service level competition among suppliers selling substitutable products to a customer that engages in supply learning. We observe how a supplier's service level performance molds a customer's ...
REVISION: The Impact of Supply Learning on Customer Demand: Model and Estimation Methodology
Date Posted:Mon, 20 Sep 2010 10:56:52 -0500
To set service levels, firms must understand how changes in service affect customer demand. Supply learning is a process whereby customers use past supplier performance to build beliefs about supplier capabilities and hence about future supplier performance. This paper presents a multi-period model of service level competition among suppliers selling substitutable products to a customer that engages in supply learning. We observe how a supplier’s service level performance molds a customer’s ...
New: Supply Chain Optimization at Hugo Boss (B) - The M-Ratio
Date Posted:Fri, 12 Jun 2009 12:17:20 -0500
We evaluate the impact of a supply chain pilot implemented at Hugo Boss. This pilot entailed altering the way in which Hugo Boss orders from its suppliers. We explore the challenge of assessing the impact of supply chain change, the link between operational performance and firm performance, and the relationship between sales, inventory, and product availability.
New: Supply Chain Optimization at Hugo Boss (A)
Date Posted:Fri, 12 Jun 2009 12:09:49 -0500
Inventory, Order management cycle, Order processing, Order quantity, Lines of business, Product management, Consumer goods, Department stores, Retail stores, Retailers, Retailing, Supply chain management, Supply chains.
Number | Course Title | Quarter |
---|---|---|
40101 | Supply Chain Strategy and Practice | 2023 (Autumn) |
Number | Course Title | Quarter |
---|---|---|
40101 | Supply Chain Strategy and Practice | 2024 (Autumn) |
Experts are charting the postpandemic supply chain. But can it be everything we need it to be?
{PubDate}A Q&A on how the pandemic has changed supply-chain operations
{PubDate}Chicago Booth’s Nicole DeHoratius expects more automation—and a new appreciation for responsiveness.
{PubDate}